Cutting line

The cutting process
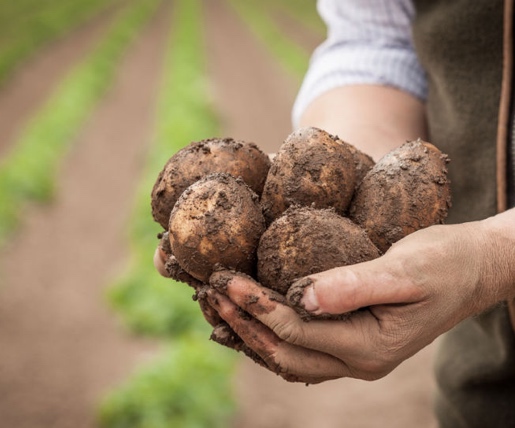
Sustainability through innovation
The Tummers cutting lines are known for their innovative character in terms of sustainability (raw material consumption, energy consumption, water consumption and waste) and quality (low failure rate, low maintenance and optimum efficiency). Our focus is on improving and making our process lines more sustainable, in order to work together with our customers on a better world.
Turnkey delivery
We can deliver your cutting line working from A to Z at your location. After commissioning, we can also train your employees in the operation and maintenance of the installations. Even after delivery, we are always there for you and we offer the best service to ensure that your production process runs as smoothly as possible.










